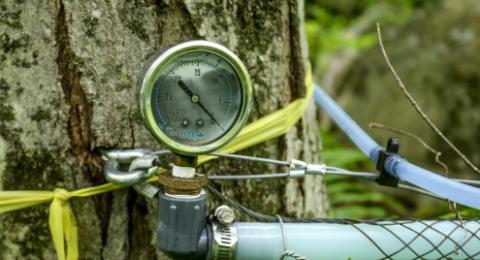
How does vacuum and atmospheric pressure affect the sap run? Examples of Tree Pressures and sap flow:
- 12-18 psi = Fair sap run
- 19-24 psi = Good sap run
- 25+ psi = Great sap run
- 15” of Hg of vacuum = 5 psi change in pressure. 20” of Hg of vacuum = 10 psi change in pressure.
- Vacuum systems turn a fair sap run into a great sap run and can increase sap yield by 50 to 100%.
- A vacuum system must be capable of producing a vacuum of 15” of mercury at the far end of the lateral tubing for it to be considered economical.
- A vacuum pump’s capacity is measured by how much air it can move in a certain amount of time – cubic feet per minute (CFM). For every 100 taps in tubing system, a pump with 1 to 1 ½ CFM is needed. If 500 taps are on vacuum, a pump with a capacity of 5 to 7.5 CFM is needed.
Designing a Tubing System – the goal is to get vacuum at the tap hole. Long spans of tubing will cover a lot of area but will have lower vacuum capabilities. Short spans will cover less area but will increase your vacuum capabilities. Sugarbushes must have a compromise between the two.
Mainlines
- 100 to 150 feet apart (up to 250 feet apart without vacuum) and less than 1000 feet (variation will occur with tap density & sugarbush dimensions). 150’ x 1000’ will cover 3.5 acres.
- Vacuum system mainlines should maintain a constant slope of 2 to 4% - a portion of the mainline under vacuum with a slope as small as ½ percent will work, but this portion must be as short as possible to maintain efficiency.
- Non-vacuum mainlines can follow steeper slopes and drainages.
- Downstream Mainline diameter should be increased when two upstream mainlines merge – usually a 1” to 1½“ increase
A well thought out vacuum tubing setup allows:
- Maximum vacuum at the tap hole.
- Leaks to be found faster.
- A single leak to have less impact on the overall tubing system.
- Faster tapping and cleaning tubing.
Mainline Sizing |
<5% Slope |
5 to 10 % Slope |
>10% Slope |
¾” Mainline Diameter |
<400 Taps |
300 to 500 Taps |
300 to 600 Taps |
1” Mainline Diameter |
<700 Taps |
400 to 900 Taps |
600 to 1100 Taps |
1¼” Mainline Diameter |
<1100 Taps |
900 to 1400 Taps |
900 to 1800 Taps |
1½” Mainline Diameter |
<1600 Taps |
1200 to 2000 Taps |
1200 to 2600 Taps |
5/16” Lateral Lines – keep lines steep, tight and as straight as possible
- With vacuum – 1 to 8 taps per lateral line.
- Without vacuum – 10 to 15 taps per lateral line. Natural vacuums can be created.
- Do not “vent” lines, instead keep them straight and tight to prevent air locks.
Tapping Guidelines
- Tap only trees 12 inches diameter at breast height (DBH) and larger.
- 1 tap hole in trees 12 to 18 inches DBH.
- 2 tap holes in trees greater than 18 inches DBH.
- Place no more than 2 tap holes per tree. The more holes, broken branches, scars, etc., the less pressure can build up in the tree.
- Drill tap holes at a slight upward angle to prevent sap pooling. Drill “check-valve” spouts at a flat angle.
- Use the smaller-diameter “health spouts” (5/16- or 19/64-inch spouts). Health spouts are preferred, but the 7/16 inch spouts are still acceptable and common when using buckets to collect sap.
- Drive spouts with care to avoid splitting the bark and wood.
- For 7/16 inch spouts, place the tap hole no more than 2 1/2 inches deep and for the smaller-diameter spouts, no more than 1 1/2 inches deep.
- Tap only white, clean wood. To avoid areas of discoloration and decay, don't place new tap holes within 6 inches horizontally and at least 2 feet directly above or below old tap holes.
- Make sure “drops” (tubing attached directly to the spout) are long enough (18” to 36”) so tap holes can be placed on all sides of the tree.
- Don't retap existing holes in any given year to expose new wood, or drill new holes to prolong the sap run.
- Don't use a tap-hole sanitizing agent.
- Remove spouts from tap holes immediately after the season. Sizing the Evaporator
Evaporator Size |
2’x33” |
2’x4’ |
2’x6’ |
2’x8’ |
30”x10’ |
3’x8’ |
3’x10’ |
4’x10’ |
4’x12’ |
5’x14’ |
Evaporation Gal/hour |
5 |
15 |
25 |
35 |
60 |
70 |
85 |
120 |
140 |
230 |
An example in sizing an evaporator by tap number:
- A good sap run will yield about 1 gallon of sap per tap
- 750 taps x 1 gal/tap = 750 gallons
- Time available each run to boil sap = 8 hours (you determine this number)
- Evaporating capacity needed = 750 gallon / 8 hours = 93.75 gal/hr
- A 3’x12’ evaporator (estimated evaporation of 100 gal/hr) would be needed
A reverse osmosis machine can remove 50 to 75% of the water from raw sap. Instead of boiling 750 gallons on a 3’x12’ evaporator for 8 hours, a producer would only need to boil:
- 188 (75% reduction of water by RO) to 375 (50% reduction of water by RO) gallons in 8 hours (an evaporation capacity of 24 to 47 gal/hr, on a 2’x6’ to 30”x8’ evaporator)
- or boil on the 3’x12’ evaporator for only 2 hours (75% reduction of water by RO) to 4 hours (50% reduction of water by RO), instead of 8 hours (without RO)
- or boil on the 3’x12’ evaporator for 8 hours with 1500 taps (50% reduction of water by RO) to 3000 taps (75% reduction of water by RO), instead of 750 taps (without RO)
Fuelwood – About 20 gallons of syrup can be produced from 1 cord of wood, or 1 cord of wood for every 80 to 100 taps.